Pillole di Innovazione
In questa sezione potete trovare alcuni approfondimenti
sui temi di Lean, Continuous Improvement ed Innovazione che
abitualmente trattiamo per supportare la crescita dei nostri Clienti
PICCOLE PILLOLE DI MIGLIORAMENTO
Metodologia Lean
Le 5S sono alla base della filosofia Lean, è applicabile a tutti i campi e tutte le funzioni.
Le 5S indica i 5 passaggi chiave per il miglioramento del processo: Seiri, Seiton, Seiso, Seiketsu, Shitsuke ed enfatizza l'uso di una mentalità e strumenti specifici per creare efficienza e valore. Implica l'osservazione, l'analisi, la collaborazione e la ricerca e la rimozione degli sprechi. Lo scopo di 5S è migliorare la funzionalità di un posto di lavoro o di una procedura (!!!) rendendo più semplice ed efficace. Ciò si verifica dando senso agli spazi, strumenti e materiali sono collocati in posizioni logiche in base a chi ne ha bisogno, alla frequenza con cui sono necessari, ecc. Se usato correttamente, 5S alla fine rende i processi più sicuri ed efficienti.
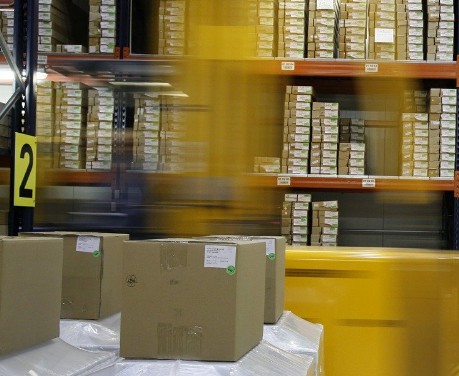
Migliorare il magazzino
Molte aziende includono nel processo di miglioramento prima di tutto la produzione e poi gi uffici in un secondo momento dimenticando il magazzino
l costo del lavoro sta aumentando in molti mercati Pertanto, molte delle nostre idee si concentrano su come aumentare la produttività all'ora di lavoro. LIl magazzino è la risorsa di bilancio numero uno nella maggior parte delle attività multicanale. L'ottimizzazione del layout del magazzino non solo migliorerà l'utilizzo dello spazio, ma aumenterà anche la produttività del magazzino e farà risparmiare denaro. Inutile dire che questo ti assicura di raggiungere i tuoi obiettivi aziendali e di deliziare i tuoi clienti con ordini che arrivano in tempo, ogni volta.
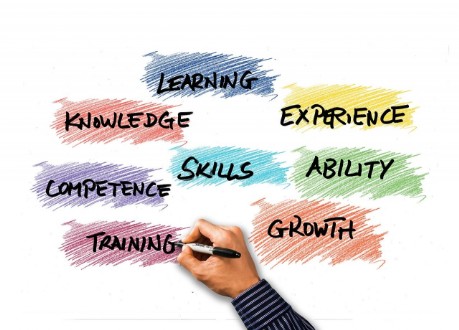
Matrice delle competenze
Sono le persone ad adattarsi al processo. Il processo è progettabile sulle esigenze dell'azienda e del mercato, le persone ... no...
La creazione di una matrice di competenze è un esercizio prezioso perché ti aiuta a comprendere le competenze e l'esperienza attuali nella tua squadra. Identifica le carenze di competenze, in cui la tua squadra manca di competenze ed esperienza. Trova aree ad alto rischio in cui ti affidi a una sola persona per completare le attività critiche. Una matrice di formazione / competenza è uno strumento utilizzato per documentare e confrontare le competenze richieste per una posizione con l'attuale livello di abilità dei dipendenti che svolgono i ruoli.
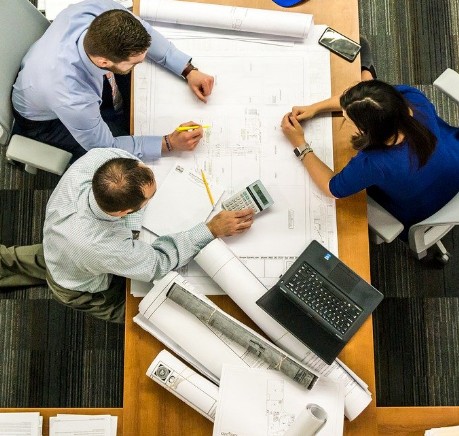
OBEYA ROOM
È considerato un componente della produzione snella e in particolare del sistema di produzione Toyota .
Durante lo sviluppo del prodotto e del processo, tutti gli individui coinvolti nella pianificazione manageriale si incontrano in una "grande sala" per accelerare la comunicazione e il processo decisionale. Questo ha lo scopo di ridurre il "pensiero dipartimentale" e migliorare metodi come la posta elettronica. L' Obeya può essere inteso come uno strumento di miglioramento dello spirito di squadra.Concettualmente affine alle tradizionali "sale di guerra", un Obeya conterrà diagrammi e grafici visivamente accattivanti che descrivono informazioni quali tempistica del programma, pietre miliari e progressi compiuti e contromisure a problemi tecnici o di pianificazione esistenti.
Magazzino post-Covid
Alcune piccole idee per ridurre i costi post-COVID
Una gestione efficiente di fornitori e magazzino influisce significativamente sul buon funzionamento di un’azienda. Inoltre, una cattiva gestione del magazzino si traduce in ultima istanza nel tenere impegnate scorte (e quindi capitale) che potresti altrimenti utilizzare per alimentare il business. Molte sono le best practice per la gestione del magazzino, in questa infografica abbiamo selezionato quelle secondo noi più significative, ovvero:
Limitare gli sprechi - Sfruttare i dati del magazzino per le iniziative di marketing - Stabilire le giuste priorità
Iniziare ad analizzare le efficienze
Sfruttare i momenti di calma valutando la produttività
L'OEE (Overall Equipment Effectiveness) è una delle "migliori pratiche" che identifica, percentualmente, quanto del tempo di produzione pianificato è veramente produttivo. Un punteggio OEE del 100% rappresenta una produzione perfetta: produzione di soli pezzi buoni, il più velocemente possibile, senza tempi di fermo.
L'OEE è utile sia come benchmark sia come parametro:
- per confrontare le prestazioni di un determinato asset di produzione con gli standard del settore, con attività interne simili o con risultati per turni diversi che lavorano sullo stesso asset.
- per tenere traccia dei progressi nel tempo nell'eliminazione degli sprechi da un determinato asset di produzione.
I KPI PER LA PRODUZIONE
Definire alcuni parametri per valutare la produttività
Con l'avvicinarsi dell'era dell'Industria 4.0 , i responsabili della produzione avranno presto accesso a più dati e informazioni che mai. Il compito dell'Operation Manager sarà quello di definire i parametri per il successo e le metriche su cui verranno giudicati tali parametri. Questo ci lascia con una domanda importante: quali metriche dovrebbero monitorare i pianificatori della produzione nell'era dell'Industria 4.0 per migliorare l'efficienza e ottimizzare i loro processi? Nell'infografica abbiamo definito 5 parametri che possono aiutare a valutare l'efficienza della produzione.
ROOT CAUSE ANALYSIS
Studiamo un metodo per l'analisi delle cause di un problema
Nel corso degli anni, molti metodi per comprendere il problema centrale alla base di un problema sono diventati parte del toolkit di analisi delle cause alla radice. Per rendere il processo più semplice, tratteremo uno dei metodi che utilizziamo con successo dai nostri clienti per ridurre i tempi di fermo macchina e migliorare l' OEE. Questo metodo in sei fasi è definito dall'American Society for Quality (ASQ). È ampiamente utilizzato nel settore manifatturiero grazie alla fiducia del settore nella familiarità con elevati standard qualitativi. Le slides che potete scaricare Vi spiegheranno come utilizzarlo per risolvere le problematiche che nascono in azienda.
TPM ( Total Productive Maintenance)
La grande idea : coinvolgere gli operatori nella manutenzione delle proprie apparecchiature ed enfatizzare la manutenzione proattiva e preventiva che getterà le basi per una migliore produzione (meno guasti, arresti e difetti).
TPM enfatizza la manutenzione proattiva e preventiva per massimizzare l'efficienza operativa delle apparecchiature. Sfuma la distinzione tra i ruoli della produzione e della manutenzione ponendo un forte accento sulla responsabilizzazione degli operatori per aiutare a mantenere le loro attrezzature.
L'implementazione di un programma TPM crea una responsabilità condivisa per le apparecchiature che incoraggia un maggiore coinvolgimento dei lavoratori dell'impianto. Nell'ambiente giusto questo può essere molto efficace per migliorare la produttività (aumentare i tempi di attività, ridurre i tempi di ciclo ed eliminare i difetti).
In questa infografica analizziamo le prime 4 colonne della TPM
A breve una nuova
interessante pillola!!!!!
A breve una nuova
interessante pillola!!!!!
A breve una nuova
interessante pillola!!!!!